Magnetic Damper -
Magnetorheological Damper
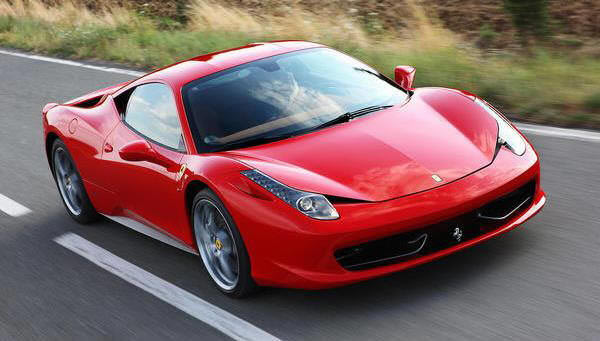
As tires become ever lower in profile and roads get ever worse, ride comfort is knife with two blades if a car is to have the sharp responses we like. Various active damping systems have promised an answer here, and none has been more impressive than Delphi’s MagneRide, the magnetorheological damper system used by Audi, Ferrari and few other mayor manufacturers.
Current car suspension systems show the result of a very long development. However, fundamentally, suspension systems remain very crude. Steel springs support the body, with a variety of linkages used to maintain the wheels in a helpful geometry during their movement. To prevent the springs simply oscillating once they have been deflected, dampers ("shock absorbers") are used to stop the spring continuing to bounce. The resistance to motion that the wheel has is therefore very much dependent on the spring rate, and the speed and stroke of damper movement.
As a result, there are frequent trade-offs required in the design of the suspension. For example, soft springing and little damping can gain excellent vibration isolation. However, such a system will bottom-out frequently on real world bumps. On the other hand, good shock reduction is achieved by a system with a relatively stiff, highly-damped system. And on smooth roads, the stiffer the suspension is, often the better the resulting handling - but such an approach is unacceptable on cars that must negotiate bumpy roads.
While active suspensions - where the entire car's mass is supported by hydraulic or pneumatic rams - were once seen as the answer, the complexity, fail-safe requirements, power consumption and weight of such systems has seen their development slowed to a crawl. Magneto-rheological dampers are answer to compromise between drivability and comfort. MR damper systems that can actively change in their damping abilities - quick enough that dive and squat, roll and pitch can be compensated for, in addition to being able to alter their behavior to suit the road and driving style.
General Motors (in a partnership with Delphi Corporation, Delphi Automotive Systems - the branch of GM) has developed this technology for automotive applications. It made its debut in both Cadillac (Seville STS build date on or after 15/1/2002 with RPO F55) as "MagneRide" (or "MR") and Chevrolet passenger vehicles (All Corvettes made since 2003 with the F55 option code) as part of the driver selectable "Magnetic Selective Ride Control (MSRC)" system) in model of year 2003. Other manufacturers have paid for the use of it in their own vehicles.
These types of systems are available from OEMs for several vehicles, including the Acura MDX, Audi TT and R8, Buick Lucerne, Cadillac CTS-V, DTS, XLR, SRX, STS, Chevrolet Corvette, Camaro ZL1, Ferrari 458 Italia, Ferrari 599GTB, Ferrari F12 Berlinetta and Holden HSV Commodore.
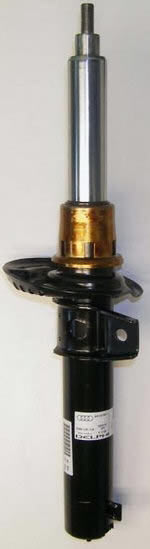
As a continuously adaptive system, it adapts the damping characteristic to the profile of the road and the driver's gear-shifting habits within just a few milliseconds. Using magnetic fields, magnetic ride adjusts the firmness of the dampers to the current driving situation within a fraction of a second. It also gives the driver a choice of basic setting for either a more comfortable or a sportier drive.
Drivers can choose between a comfortable and a sporty driving mode to suit the driving situation and their personal tastes. In both modes the suspension’s damping forces are continuously adjusted to the current driving situation to produce uncompromising road behavior. The benefits are clearly appreciable both in terms of comfort and handling characteristics. In the normal mode – when the oil is more viscous and the degree of damping less pronounced – the car rolls surprisingly smoothly; this is ideal for long-distance driving or uneven road surfaces. In the Sport mode, by contrast – when the oil is less viscous – it reveals an extremely dynamic character that is manifested by a resolutely firm grip of the road surface. Rolling movements are suppressed from the very moment the steering is turned even more effectively than in the basic suspension setting, and the steering response is further improved. The self-steering behavior is further optimized by the specific stabilization provided for each individual wheel, resulting in a driving feel reminiscent of a go-kart.
Magneto-rheological fluids and its close relative electro-rheological - ER - fluid have been around since I think the mid 1940s. I remember first reading about it in the early 80s. It has a complex name but it involves a concept that's quite simple to understand.
A control unit computes the optimum damping force for the individual driving situation. It does so using information from the wheel travel sensors and communication with other systems such as the steering and ESP.
Since no mechanical parts must be moved, the MR damper responds extremely spontaneously. The damping force is only dependent on the power applied to the magneto-rheological fluid and can be adjusted up to 1,000 times a second. Thanks to the variable control of the power, the damping force can also be set infinitely. This means the magneto-rheological dampers respond almost in real time with great sensitivity to impulses from the road. The control system loop with Skyhook algorithms ensures the greatest possible road-to-wheel contact in the case of uneven road surfaces with the least impulses to the car body. This means the car with Magnetic Ride has the greatest possible driving dynamics and allows for comfort.
Delphi’s magneto-rheological monotube damper requires roughly the same space requirements as conventional dampers or struts. If required, Delphi supplies the complete semi-active system with dampers and struts including the sensors and the control unit.
Rheology is a science that studies the deformation and flow of materials. Rheological fluids have flow characteristics that can be changed in a controllable way using electrical current or a magnetic field. Depending on the base fluid and the strength of the electrical current or magnet, the fluid's viscosity can be varied from thinner-than-water to almost-solid and any stage in between. The fluid's response is instantaneous, completely reversible and extremely controllable, but there are some limits.
Electro-rheological (ER) fluid changes viscosity when an electric current is applied directly to the fluid itself. ER fluid was first invented and patented in the 1940s, and to varying degrees, development has continued ever since. It has been tested in a wide range of applications, from torque converters, clutches and dampers to synthetic muscles and dampers in powered prosthetic arms and legs. It works, but its shear strength (its resistance to shearing movement) is limited. Despite huge investments in research and development, ER fluid is still far from ready for any practical applications.
Magneto-rheological (MR) fluid on other side has shear strength about 10 times stronger than ER fluid. Invented at the same time as ER fluid, the two have many similarities. Both can use oil, silicone, water or glycol as the base fluid, and both contain polarizable particles suspended in the fluid. Polarizable means the particles can be forced to align in a specific way. These suspended polarizable particles are the basic difference between ER and MR fluids. ER fluid uses particles that polarize when directly exposed to an electric current. MR fluid uses somewhat larger particles of iron that polarize when surrounded by a magnetic field.
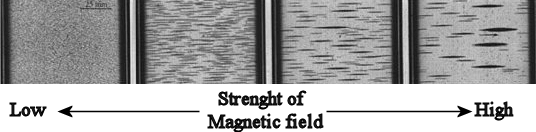
The typical MR fluid particles are soft iron spheres or ellipsoids measuring 3 to 5 microns (3 to 5 thousandths of a millimeter) in diameter. Depending on the application, the fluid will be 20 to 40 percent saturated with the iron particles, and other additives will be used to control particle settling and mixing, fluid friction and fluid viscosity. Nanoparticles are covered with protective polymerous macromolecular coating, so-called surfactant (surface active agent), that prevents a direct contact between nanoparticles and causes repulsive forces between them. Specific gravity is generally between 3 and 4; for reference, water's specific gravity is 1. Thus, a 200 liter drum of MR fluid can weigh almost a full ton. MR fluids are developed specifically for the application intended. For instance, in addition to automotive uses, MR fluids have been developed for use in dampers that protect buildings and other structures from earthquake damage. These dampers sit still for long periods, so different additives are needed to keep the particles in suspension.
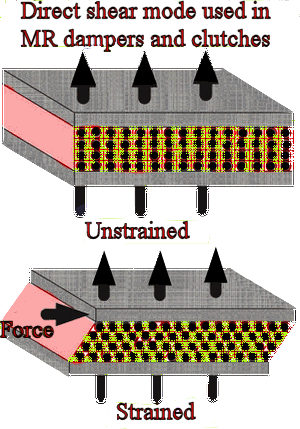
If a very thin layer of MR fluid (eg 0.15 - 0.3 millimeters) is placed between two electro-magnetic plates - and then the plates are slid relative to one another - the MR fluid is said to be operating in 'shear mode'. Such method can be used for the production of clutches and brakes.
A similar set-up - but this time with the plates being pushed towards one another - is termed 'squeeze mode'. This approach can be used for damping very small movements.
But of most interest to us is 'valve mode'. This is where there is a flow of MR fluid from one reservoir to another, with the connection being through a small diameter passage. If the passage is subjected to a variable intensity magnetic field, the amount of fluid that is able to flow will be altered. In effect, the fluid will act as if the opening changes in size. This approach is used in MR fluid damper design.
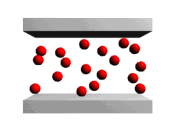
The strength of the bonds between the magnetized iron particles causes the viscosity of the fluid to apparently increase. The magnetized fluid is not, technically, more viscous, but it is more resistant to passage through the restrictions in the damper because the concentration of magnetized fluid forms a kind of deformable plug.

When a magnetic field is applied to a coil – by means of a pulse delivered by a control unit, the micron-sized particles dispersed inside oil used in car dampers (basic synthetic hydrocarbon oil, polymer liquid, mineral oil or silicone-based fluid), align themselves along the magnetic lines of force and magnetic particles are aligned against the direction of movement of the damper. Just like the iron filings that the science teacher used to shows lines of force around a bar magnet, the iron particles within the fluid form a pattern. In each of the monotube dampers are a piston containing two electromagnetic coils and two or more small fluid passages through the piston. The electromagnetic coil is integrated into the damper piston in such a way that when it is energized the magnetic flux runs exactly transversely to the admission ports in the damper piston. The electromagnets are able to create a variable magnetic field across the fluid passages and field can be altered in strength to adjust the damping force in just 100 nanoseconds. When the magnets are off, and the piston moves inside damper body, the fluid travels through the passages freely.
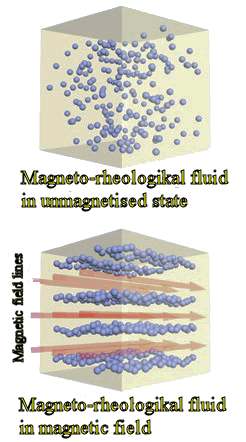
However, when the magnets are turned on, the iron particles in the fluid create a fibrous structure (so called magnetoviscous effect) through the passages in the same direction of the magnetic field. If the piston moves, the particles aligned in strings like pearls on a necklace, create flow resistance in the flowing suspension fluid. If, in order to flow, the 'necklaces' need to be broken, the fluid acts as if its viscosity has increased. In fact the carrier fluid - let's call it just oil for simplicity - hasn't increased in viscosity at all, but the combination of the iron and the oil behaves in a more viscous manner. This allows the firmness of the dampers to be increased or decreased within a fraction of a second or gradually. Altering the strength of the current results in an instantaneous change in force of the piston. If the sensors sense any body roll, they communicate the information to the ECU. The ECU will compensate for this by changing the strength of the current to the appropriate dampers. This alters the characteristic of the damping much faster than is the case in conventional adaptive dampers and provides the right degree of damping force at each individual wheel in every situation.
The greater the energy applied and the stronger the magnetic field, stronger the “necklace“the greater the resistance and damping power. The energy is controlled in relation to driving dynamics and impulses from the road. This means for every road situation optimal damping power is available. This damping power produces – according to OEM desire – a more comfortable feel or sportier vehicle handling. In theory, the viscosity of the damper liquid can be changed to an almost solid state similar to plastic or rubber in composition. As the viscosity of the liquid changes, it offers a difference in the damping.
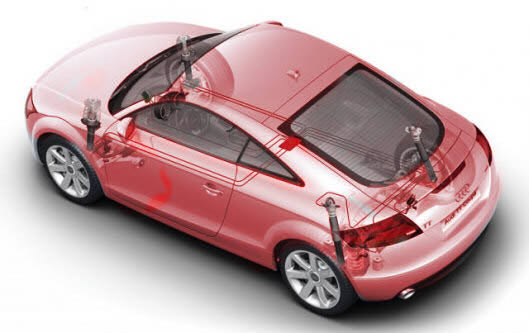
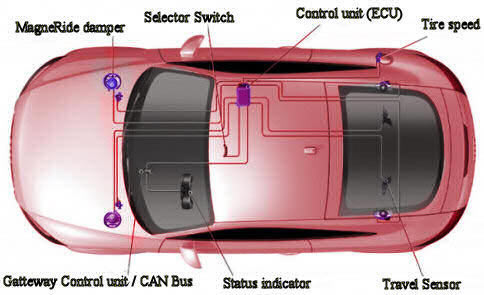
Magnetic suspension is described as the fastest reacting suspension in the world as sensors monitor the road surface up to 1000 times per second and an ECU can make variations within a millisecond resulting in the possibility of multiple damping variations being made in a fraction of a second.
Each of the four dampers is adjusted individually and independently even when it seems that all of them are doing the same thing. This ensures a comfortable ride along various road surfaces. Magnetic suspension reduces vibrations, bouncing, noise and body roll very effectively on all road surfaces and at any speed that the vehicle could travel. The reduction of body roll may reduce the need for anti roll bars. Although this type of suspension offers a very comfortable ride, sport settings can be applied or tuned into the system to cater for performance vehicles. Low energy requirements of the system are another benefit. On average, a damper requires just 5 watts of electrical power (25 watts at a maximum).
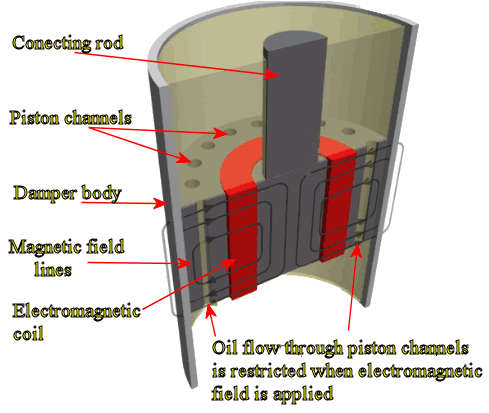
Magnetic dampers are designed with similar dimensions and connection points to other types of dampers so they are usually attached to the chassis of the vehicle similar to how a coil spring suspension would.
The MagneRide controller itself is a stand-alone unit equipped with two parallel processors: one for input signals and one for output. It operates the shocks on 5 volts DC that is pulse-width modulated to adjust current to the magnets. Current draw can spike momentarily at about 5 amps per shock, but normal current draw is about half that much, and there is always some current flowing whenever the key is on.
A magnetorheological car damper is controlled by algorithms specifically designed for the purpose. There are plenty of alternatives, such as Skyhook or Groundhook algorithms. The idea of the algorithms is to control the viscosity of the magnetorheological fluid with electric current in the best possible way. The control module uses suspension height data supplied by position sensors at each corner. With throttle position sensor (TPS), transmission and wheel speed data supplied by the Powertrain Control Module (PCM), the suspension controller can predict lift and dive at each end of the car and operate the shocks' "valves" to counteract it. With data from a steering wheel position sensor, a two-plane acceleration sensor and a yaw rate sensor, the shocks can be operated as needed to control body roll during any maneuver. The system also checks body movement during antilock brake system (ABS) operation using vehicle speed, wheel speed and other data supplied by the ABS control unit. All in all, control module are constantly checking yaw, pitch, roll and heave of the car and continuously adjusting dampers.
Like earlier versions, this is a semi-active suspension system. In addition to its main function of keeping the wheels in contact with the road, it can check body motions and, within certain limits, adjust weight bias at each corner by preventing suspension compression. But it is a reactive system, not proactive, and it cannot extend the suspension to make the car lean into a turn. Still, it provides a significant amount of increased control with base settings that are tuned for a more comfortable ride.
You will likely not see this in the Aftermarket any time soon, though there are people working on it.
At this moment the cost is too prohibitive. Not only is the fluid expensive, but damper computer control system must be completely integrated with the car and car’s ECU. Hardware is not a problem, it's the software that makes all the cool stuff happen, but is also what takes the longest to develop at the greatest cost. Because of all that modern car system integration it’s very hard to implement aftermarket magnetic damper system and interface it to existing car system.
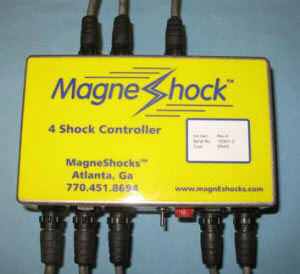
You can make some of this exotic stuff at home. Just mix some powdered iron filings with a thick liquid like corn oil, and presto: a simple MR fluid. Hold a magnet nearby and the bits of iron will line up end-to-end; they form a rigid lattice that stiffens the mixture. Take the magnet away and the fluid will relax again.
Put bit of a MR fluid on the plate and magnet under it and things get strange. The interaction of the magnetic field, the surface tension of the ferrofluid and gravity results in the formation of stable spikes of liquid. The spikes are still liquid - touch one and you'll just get an oily finger - but if you don't move the magnet, they look like a solid sculpture.
The stronger the field, the smaller the spikes. In the weedy field from a ferrite magnet you'll get just a smooth mound of fluid with a few spikes where the field is strongest, but the spikes get a lot smaller when you're playing with one of the bigger neodymium magnets.
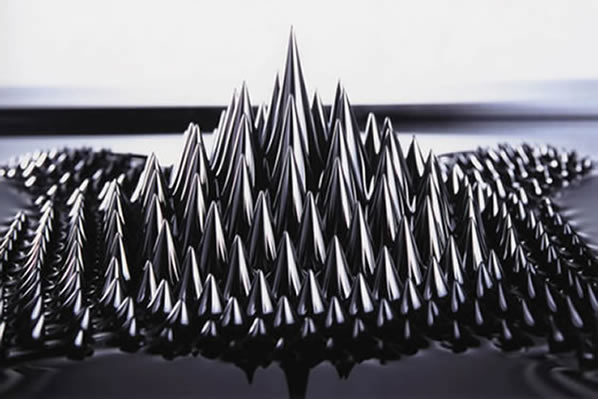
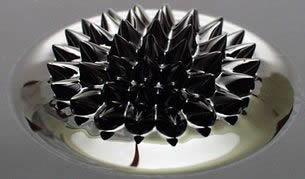
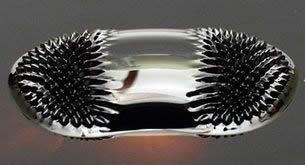
With reference to
http://www.formula1-dictionary.net/damper_magnetorheological.html